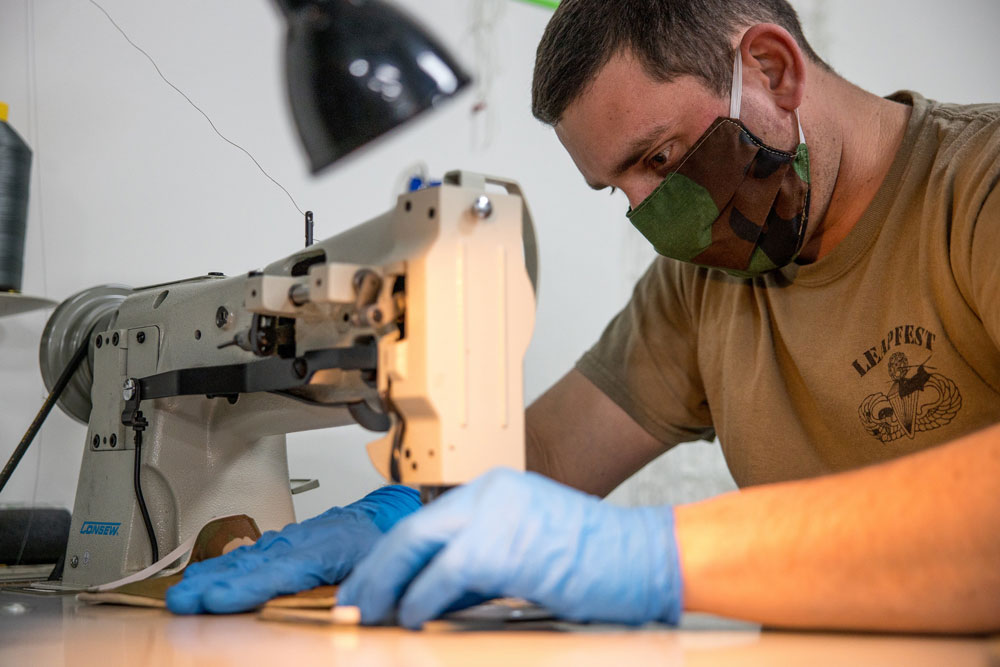
April 6, 2020; CityLab
As the coronavirus crisis grows across the US, many goods seem to be in short supply; we’ve all seen the jokes about toilet tissue becoming the new US currency. It’s less funny when the shortages affect things like personal protective equipment and face masks, which are recommended by the Centers for Disease Control to stem the virus’ spread.
Governments and healthcare facilities have asked that N95 masks and other more robust equipment be reserved for hospitals, where healthcare workers come into close contact with the virus and are woefully underequipped to protect themselves. But a week after the CDC recommended that everyone wear a basic face mask, those too are hard to find.
The response of citizens across the country represents the attitudes and energy on which the nonprofit sector was built. Thousands of people jumped into action and began sewing masks and making other equipment for donation.
Multiple major news outlets, including the Washington Post, HuffPo, and National Geographic, issued instructions or guidance for making masks and other personal protective equipment (PPE) at home. Most masks include two cotton panels and a pocket into which one can insert a disposable filter.
It’s not just masks, either; Kriston Capps at CityLab highlights Maryland Made to Save Lives, a manufacturing network that sprang up in response to the crisis to coordinate supply chains with manufacturers and expedite the production of protective equipment. Maker spaces are using 3D printers to churn out face shields or respirator components for hospitals. Fashion designers are switching over to making hospital gowns.
Sign up for our free newsletters
Subscribe to NPQ's newsletters to have our top stories delivered directly to your inbox.
By signing up, you agree to our privacy policy and terms of use, and to receive messages from NPQ and our partners.
“There was an overwhelming response to the call,” said one member of the Maryland network. “I think it’s one of few cases where we’ve had a similarly exponential response to the virus. One person wrote multiple people, and they wrote multiple people.”
A few years ago, James Fallows at the Atlantic chronicled the rise of the “Maker Movement,” a rise in US-based, small-scale manufacturing thanks to new tools like 3D printers and smaller, less expensive laser cutters.
This volunteer surge, though it is partly made possible by the rise of that movement, more closely resembles things NPQ has chronicled like the student mutual aid networks or the pivoting of volunteer databases to connect nonprofits with willing virtual hands. Thousands of citizens with sewing machines and extra time on their hands have stepped into the void of government action; some are selling their products, and others are donating it for free.
No one is under any illusions that this volunteer effort is enough to compensate for the chaos at state and federal levels, as governments outbid each other for dwindling supplies of PPE. “Makers know they can’t turn the tide,” writes Capps. “They aren’t able to match the level of mobilization envisioned by the Defense Production Act, the Korean War-era law that the Trump administration has used (however falteringly) to order American factories to start churning out ventilators and respirators at scale.”
But every bit helps; every mask worn reduces the risk of contagion just a little. When so many people are feeling trapped and helpless against the virus’s spread, this mutual aid effort gives citizens agency. This impulse to engage with solutions at any level should be seen as a new opportunity to engage communities in more extended political and rebuilding efforts.—Erin Rubin