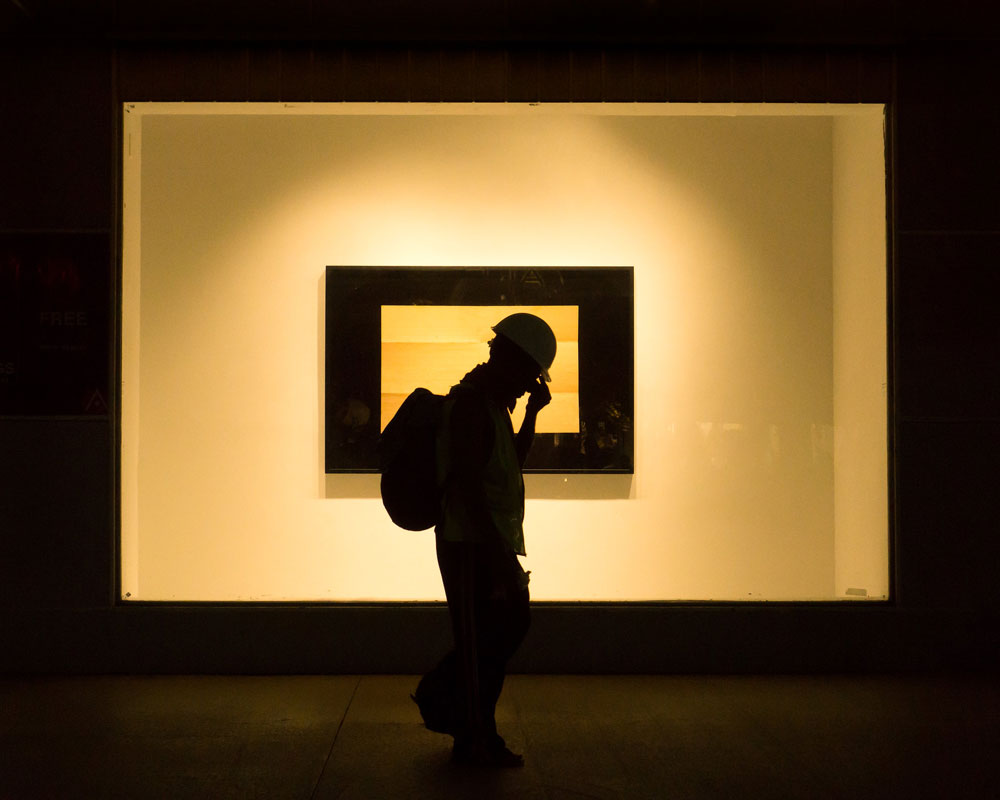
November 6, 2019; New York Times
The tech startup run by Lasse Rheingans has captured the attention of the Wall Street Journal, which recently reported on his unusual approach to productivity. Employees work daily from 8 am to 1 pm four days a week—and never after hours. He is betting his business on the hypothesis that this will make people work harder and in more effective and concentrated ways.
Rheingans insists his employees leave their work phones at work, and he blocks access to the company network on off hours. Employees are also to check email only twice a day.
Cal Newport, who writes about this radical idea in an opinion column in the New York Times, authored a book entitled Digital Minimalism: Choosing a Focused Life in a Noisy World, so it comes as no surprise that he says, “Yes please!” to this notion.
Actually, he says far more than that. He implies that we are such novices in our new knowledge era that we do not yet get how to pace ourselves, despite the fact that the indicators of a system seriously out of balance are everywhere. But he suggests we forgive ourselves for that, writing, “The history of technology and commerce teaches us that we should be skeptical of the idea that we’ve somehow figured out the best way to conduct knowledge work in the network age in such a short time.”
Consider an analogous revolution: the slow evolution of complex manufacturing. As late as 1913, Henry Ford, like most other automakers at the time, still built cars using the “craft method,” in which each vehicle was constructed in a fixed spot on the factory floor, with workers bringing over the various pieces needed for its assembly. Complex components like the magnetos were still constructed by hand by a single skilled worker at a stationary work bench. Cars at this point, in other words, were still being put together in largely the same way that Karl Benz built the first practical automobile three decades earlier.
Sign up for our free newsletters
Subscribe to NPQ's newsletters to have our top stories delivered directly to your inbox.
By signing up, you agree to our privacy policy and terms of use, and to receive messages from NPQ and our partners.
The craft method of manufacturing was simple and convenient—directly scaling up the natural approach artisans had always used to assemble complex artifacts. But then Ford launched a series of bold experiments to explore approaches to this work that would trade simplicity and convenience for vastly more effectiveness. These experiments, of course, were successful. In early 1913, the labor time required to produce a Model T was around 12½ hours. By 1914, after Ford instituted the continuous-flow assembly line supported by specialized tools, this time dropped to only 93 minutes.
I believe that knowledge work today is where automobile manufacturing was in 1913. The way we currently work is simple and convenient. Because everyone can talk to everyone at any time through email and instant messages, we just let workflow along as an unstructured conversation made up of missives flying back and forth through the electronic ether. This scales up the way we’ve always naturally collaborated in small groups.
But, he writes, Rheingans is attempting to reinsert a little calm forethought into this frenzy of digital convenience. He argues it is both arrogant and ahistorical to believe we have figured our approach to work in this new era out so early in the game.
“I suspect,” he concludes, “along with Mr. Rheingans, that among other transformations it will reject the idea that always-on electronic chatter is a good way to efficiently extract value from human minds.”
He admits that Rheingans may or may not be on to something, but “what is right in this case is the exploratory mindset that led to these experiments in the first place.”—Ruth McCambridge